The steel industry faces many challenges due to rising energy demands, continuous price increases for natural gas & raw materials, and the steadily decreasing quality & quantity of iron ore. The conventional blast furnace route is both costly and energy intensive, making it difficult to fulfill ever stricter environmental regulations and achieve sustainable economic competitiveness. To combat these issues, POSCO worked to develop its own iron-making process that could be eco-friendly, cost effective, and efficient.
The FINEX¢ç Process
The FINEX¢ç Process was jointly developed by POSCO in Korea and Primetals Technologies in Austria. FINEX¢ç (along with COREX¢ç – another smelting process developed by Primetals) is the only commercial proven alternative steelmaking process to the blast furnace (BF) route.
FINEX¢ç is based on the direct use of iron ore fines and non-coking coal while eliminating the coke-making and sintering processes, which are most critical to the conventional blast furnace process. Combining these two decisive advantages leads to lower production costs and the reduction of environmental emissions in comparison with the conventional blast furnace route.
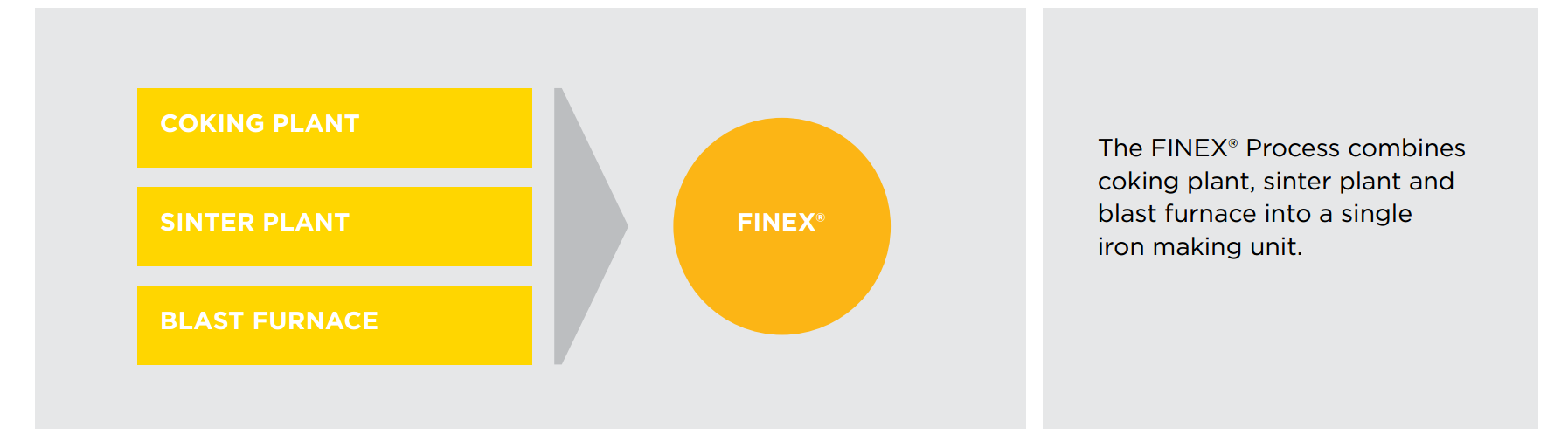
The FINEX¢ç Process combines cooking plant, sinter plant, and blast furnace into a single iron making unit.
Advantages of the FINEX¢ç Process
There are several key advantages to and differences in using the FINEX Process:
- Non-coking coal can be used directly as a reducing agent and energy source
- 100% fine ore can be directly charged to the process; no sintering or pelletising is required
- Pure oxygen can be used instead of nitrogen-rich hot blast
In addition, the FINEX¢ç Process offers several key advantages over alternative BF methods.
- Economic benefits – low investment and operational costs due to the elimination of coking and sinter plants
- Ecological benefits – lowest process-related emission rates
- Product quality – hot metal quality suitable for ecological steel applications
- CO2 mitigation potential – pure oxygen is used
- Resource preserving – directly uses a wide range of iron ores and non-coking coals
- Beneficial by-products – generation of highly valuable export gas for various purposes (electric power generation, DRI production, or natural gas substitution)
- The FINEX¢ç Process combines coking plant, sinter plant and blast furnace into a single iron making unit.
Creating The FINEX¢ç Process
Starting in December 1992, POSCO and Primetals Technologies signed a cooperation agreement for the joint development of the FINEX¢ç Process. Following initial laboratory, bench scale and pilot plant tests, the FINEX¢ç F-0.6M Demonstration Plant, with a nominal capacity of 2,000 tons per day, was built in Pohang, Korea, and started up in May 2003. On the basis of successful results and optimization of equipment and process parameters over the past few years, POSCO developed their own independently designed program in February 2017. Designed to carry out overseas FINEX projects without relying on Primetals Technologies or other external resources, the program can be used to calculate core equipment specifications and raw material conditions. In particular, the development of the FINEX Process Design Program, one of the subprograms, has made it possible for the ¡°heat & mass balance¡± to be automatically calculated when raw & fuel material conditions change.
[clickToTweet tweet=¡±The FINEX¢ç Process is a cost-effective, more eco-friendly, and efficient way to make steel. ¡± quote=¡±The FINEX¢ç Process is a cost-effective, more eco-friendly, and efficient way to make steel. ¡± theme=¡±style6¡È]
Efficiencies of the FINEX¢ç Process
The FINEX¢ç smelting reduction process is one of the most exciting iron making technologies on the market. It is distinguished by the production of high-quality liquid hot metal, on the basis of directly charged iron ore fines, and coal as the reductant and energy source. A key feature of the FINEX¢ç Process is that iron production is carried out in two separate process steps. In a series of fluidized-bed reactors, the fine iron ore is reduced to direct reduced iron, compacted (HCI), and then transported to a melter-gasifier. Coal and coal briquettes charged to the melter-gasifier are gasified, providing the necessary energy for melting in addition to the reduction gas.
The FINEX¢ç Process is Environmentally Friendly
The FINEX¢ç Process and the blast furnace route are coal-based processes reducing iron ore to iron, which is subsequently melted into hot metal. In both processes, the same product is generated out of almost the same raw material. A question that arises – and not only from an economic point of view – is ¡°how do these production routes deal with unwanted impurities?¡±
A certain amount of environmentally harmful substances is inevitable based on the raw material mix. Hence, the objective of a sustainable steelmaking process is to discharge these substances in an environmentally compatible condition or destroy them during the process itself. Since the FINEX¢ç Process captures most of the pollutants in an inert state in the slag, and the released hydrocarbons are destroyed in the dome of the melter gasifier, no additional investment or operational costs are incurred for a complex gas or disproportional waste water conditioning plant.
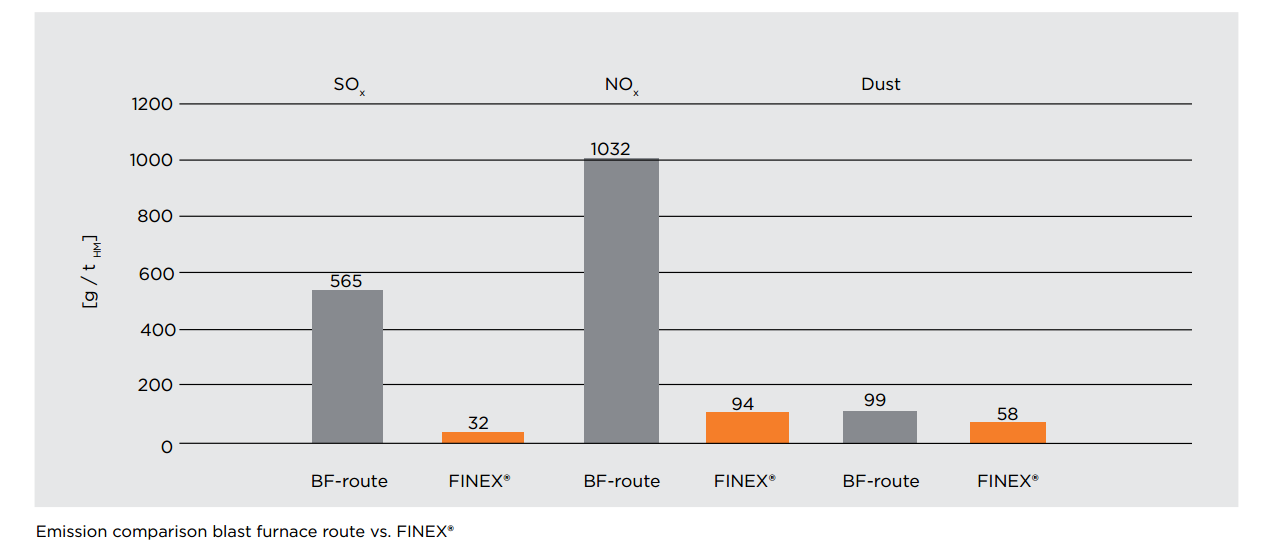
Comparing the traditional blast furnace with the FINEX Process shows the improvements that POSCO was able to achieve to be more
environmentally friendly.
Future-Proof Emissions Figures
To bring blast furnaces in line with current and expected environmental standards, plants require significant investment. This can already be seen in the case of blast furnace dust emissions that are efficient, but costly filter systems must be installed in the sinter and coking plant. The FINEX¢ç Process values are already far better than expected future standards. Moreover, the full development potential of the FINEX¢ç Process has not yet been realized with respect to a further reduction of emissions.
Moving Forward with Greater Potential
Because the FINEX¢ç Process is still being optimized, additional economic and technological benefits are anticipated. Major developments are continuously being carried out to increase efficiency. The latest achievements include breakthroughs in the field of heat recovery, dry dedusting, and outstanding performance improvements. Based on the well-proven plant concept, new process features, the highly competitive production costs, and environmental features, Primetals Technologies and POSCO are confident that the FINEX¢ç Process will account for an increasing share of future investments in iron making facilities.
*Cover image courtesy of the World Steel Association
Don¡¯t miss any of the exciting stories from The Steel Wire – subscribe via email today.