l ¡®Steel E-Motive(SEM)¡¯ – New concept of the autonomous vehicle development project
POSCO is working with member companies of WorldAutoSteel*, a consortium in the automotive sector under the World Steel Association, to develop a fully autonomous vehicle concept.
The ¡®Steel E-Motive (SEM)¡¯ project, which started in earnest in June 2020, is for future mobility as a service (MaaS)**, and the key is to deliver a new vehicle architecture. It is being carried out as a 30-month large-scale project with steel companies from 18 countries around the world, and ¡®Ricardo¡¯, a UK-based automotive engineering company, took charge of engineering and design.
WorldAutoSteel launched this project to show that Advanced High-Strength Steel products and various steel technologies can be the best solution for the design and engineering of MaaS vehicles and proposed a MaaS vehicle concept as an advanced fully autonomous electric vehicle that can be manufactured anywhere in the world.
**MaaS (future Mobility Service): Abbreviation for ¡®Mobility as a Service¡¯, which means ¡®Mobility as a Service¡¯. The core of MaaS, called next-generation mobility, is the ¡®integration of all transportation¡¯, which means that services such as routes and payment of individual transportation are bundled into one platform.
l How COVID-19 changed the MaaS project
In the early stages of the future transportation development project, due to the prolonged COVID-19 pandemic, the WorldAutoSteel management team and Ricardo¡¯s engineers and design teams had to quickly re-adjust the direction of the project that was initially planned.
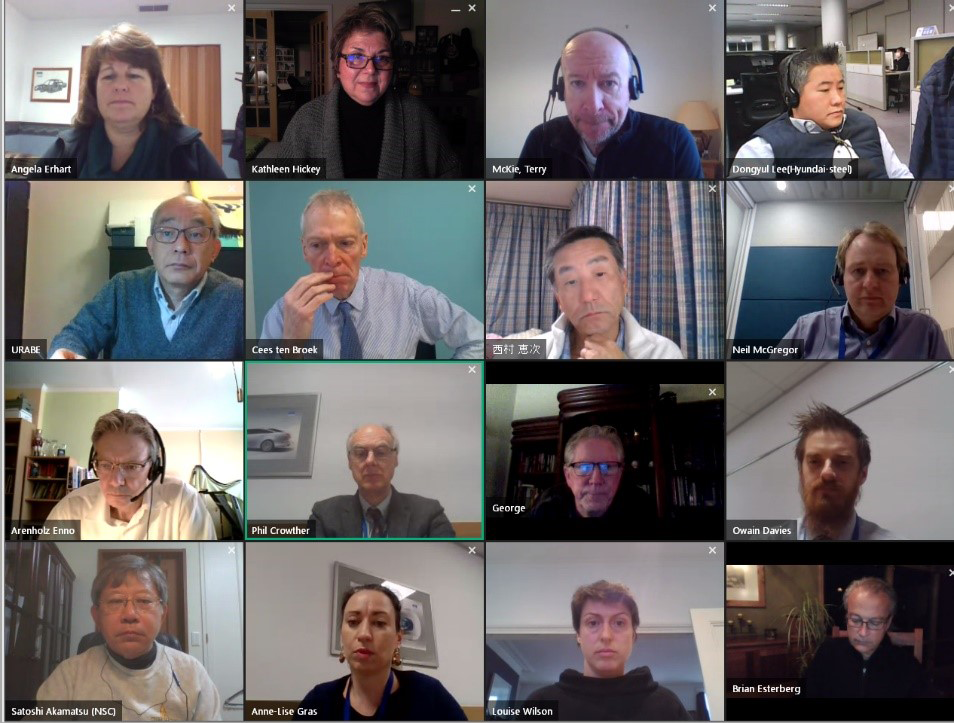
¡ã The Steel E-Motive team had to quickly adapt to remote working
¡°We started the project by completely transforming to remote cooperation instead of face-to-face meetings with 18 steel companies to ensure that our schedule was not disrupted,¡± said Anne-Lise Gras, SEM project manager from Ricardo. She shared her thoughts at the time when she was thinking about efficient project management methods.
As the project progressed smoothly due to the synergy effect among the consortium members, two models of the concept of a fully autonomous MaaS vehicle were derived: a ¡®4-passenger variant for intra-city use¡¯ and a larger ¡®6-passenger extra-urban variant¡¯. The project demonstrated the suitability of the latest Advanced High-Strength Steel (AHSS) grades and fabrication processes for use in a fully autonomous vehicle. The vehicles are conceptual and virtual, but the level of validation could facilitate a future prototype build, depending on industry interest and feedback.
l The power of high-quality teamwork
Dean Kanelos, Vice Chair at WorldAutoSteel from Nucor Corporation, said that the key to the success of the SEM project is high-quality teamwork.
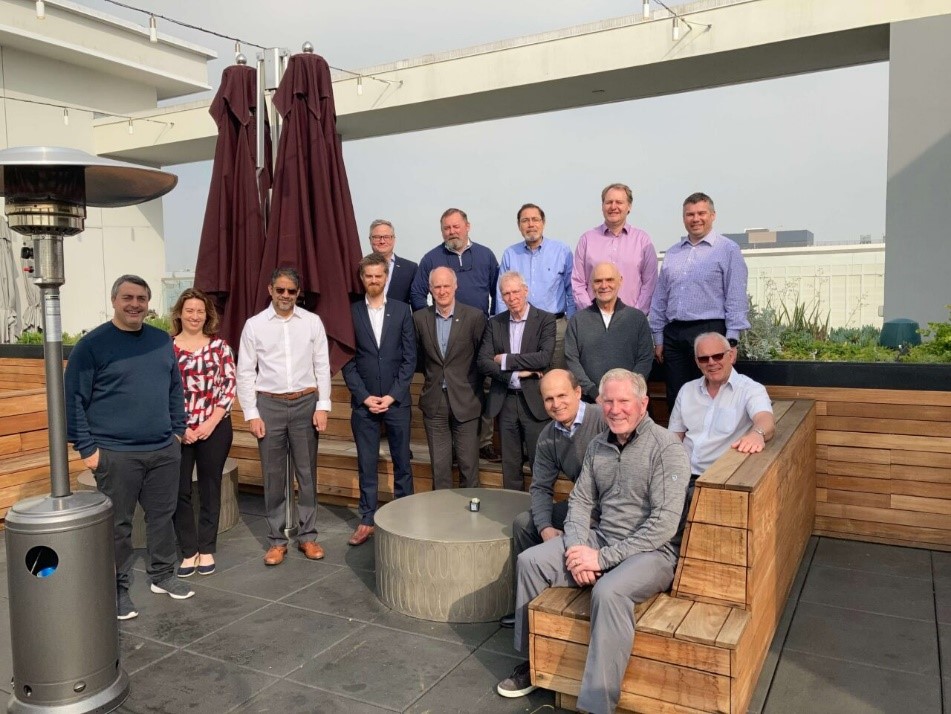
¡ã The high level of teamwork has made the Steel E-Motive program possible
While meetings were mainly held remotely during the project, several face-to-face meetings were a breakthrough and had a positive impact on the project. In particular, the first face-to-face meeting held in March 2022, two years after the pandemic struck, was a meaningful time.
Anne-Lise Gras, SEM Project Manager from Ricardo, said, ¡°We held the meeting in Los Angeles because Pacific Coast time enabled engagement with Asian members who were not authorized for international travel. It was able to elicit feedback that was different from remote meetings, and raised the cooperative relationship that had been built through online meetings to the next level.¡±
l POSCO shares experience and knowledge as a SEM team member
WorldAutoSteel member POSCO is one of the 18 members actively collaborating on the Steel E-Motive project. Jae-hyun Kim and Hae-a Lee, senior researchers for the Materials Forming Research Group at POSCO¡¯s Steel Solution Research Lab played a decisive role in resolving the numerous design difficulties faced in this project. Jae-hyun Kim, a senior researcher at POSCO said, ¡±I would describe the project as being pioneering – drawing a picture of mobility as a service transport solution for an uncertain future. It was important to let many thoughts emerge from various perspectives rather than just one¡¯s own biases.¡±
In addition, the workshop held face-to-face in Munich, Germany on November 21st, was considered a successful collaboration case, and he added that it was because in-depth discussions on body design issues were conducted and important decisions were made. In particular, it led to positive results in successfully deriving a body design for SEM vehicles.
The POSCO team ran a complimentary research project that contributed in several ways, including topology optimization on the body structure design, analyses of solutions to reduce cost and mass while maintaining crash performance, and a review of whether significant parts of the Steel E-Motive vehicle body could be manufactured by roll stamping, a new and innovative manufacturing method, which was actively reflected in the project and greatly contributed to deriving the optimal design solution.
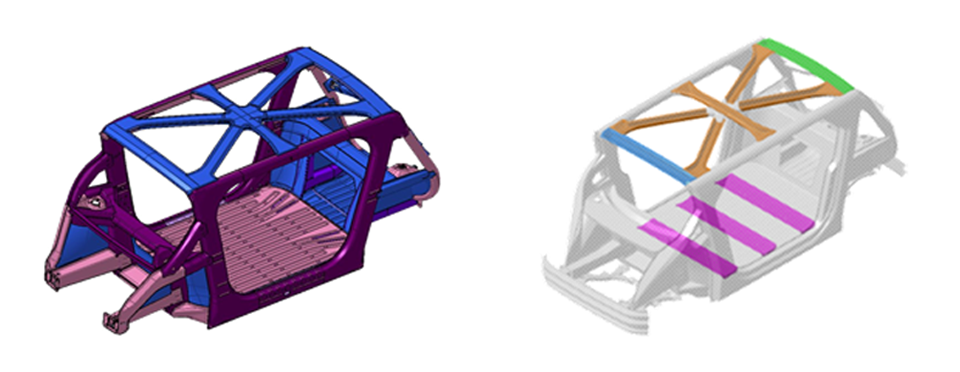
¡ã SEM body structure with Advanced High-Strength Steel (left) and 10 types of parts with roll stamping, POSCO¡¯s unique method (right)
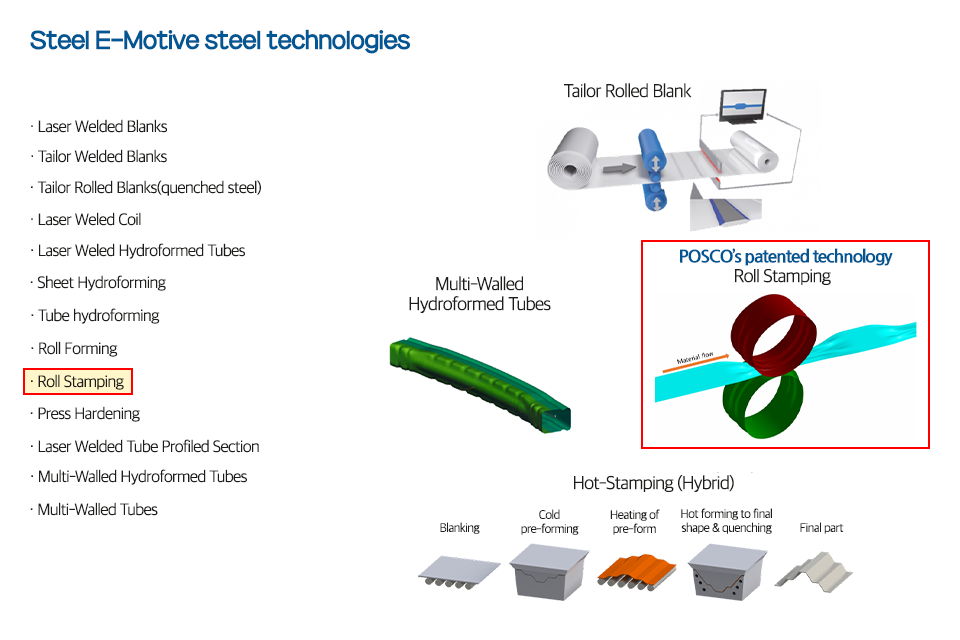
¡ã POSCO¡¯s patented technology ¡®Roll Stamping¡¯ is included in the SEM project¡¯s candidate list for parts manufacturing method (Source: ahssinsights.org)
l High-quality collaboration creates a high-quality end product
The foundation for the success of this project can be said to be the know-how and trust accumulated through the capabilities and experiences of each team member. Neil McGregor, Ricardo Chief Engineer on Steel E-Motive, is responsible for ensuring that the engineering aspect of the project and all the technical targets are delivered. He said that building trust has been important. Members of the consortium steel company in the automobile sector actively shared their expertise and experiences even though they were all competitors. Satisfying results were obtained thanks to the ideas from various perspectives differentiated from existing vehicles, such as vehicle production, styling, crash performance, sustainability, and selected materials.
Neil McGregor, Ricardo¡¯s Chief Engineer, said, ¡°We were able to solve the technical challenges thanks to the high level of teamwork made up of expertise in steel. We had WorldAutoSteel members and expert advisors who are very knowledgeable about the entire portfolio of steel grades and properties, and then we¡¯ve got other members who are experts on steel welding, joining, and fabrication.¡± George Coates, WorldAutoSteel Technical Director and Steel E-Motive Program Manager said, ¡°The integration of our member expertise with Ricardo¡¯s engineering and design talent have achieved vehicle concepts that we¡¯re extremely proud of and can only be realized with steel technology¡±.
The Steel E-Motive team is continuing to work through 2022 on this project in the run-up to the launch of the final virtual concepts in 2023. Next year, all of the teamwork will pay off as these concepts are handed over to WorldAutoSteel members and the consortium members will then perform technical transfers with their customers, to inform them of how Advanced High-Strength Steel delivers. It¡¯s expected that the engineering concepts embodied in the Steel E-Motive program will be adopted or adapted for future autonomous vehicle designs.